Featured Products
- ⅛"~12" (3-300mm)
- Liquids and Gas
- -40~300°F (-50~150°C)
- +/-0.1,0.15,0.2 and 0.5%
- Any
- 3600PSI (25Mpa)
- SS304, 316SS 316L
- 4-20mA, pulse, MODBUS, HART
- ANSI, DIN, JIS, Wafer, Sanitary, Threaded
- All industires, custody transfer, multi-outputs (water cut, density, temperature, mass and volume and many more)
- ½"~12" (15~300mm)
- Steam, Liquids and Gas
- -40~662°F (-30~350°C)
- 1.5% gas/steam, 1% liquids
- 1 to 10 cst
- 920PSI (6.4Mpa)
- SS#304 std., SS #316 opt.
- 4-20mA, pulse, MODBUS, HART
- flanges (ANSI, DN, JIS)
- Full compensated mass flow, no need to adjust output due to changes in pressure and/or temperature
- ¼"~unlimited (6mm-unlimited)
- All gases
- -23~482°F ( -5~+250℃)
- 1% of reading plus 0.5% FS
- Not Applicable
- 1000PSI (69 bar)
- SS #316
- 4-20mA, pulse, MODBUS, HART
- NPT and flanges (ANSI, DN, JIS)
-
Any gas measurement requiring both standard volume or mass
- Unlimited
- Gas, Liquid, Steam
- -22 ~+480°F (-30~ +250°C)
- ±0.075%, ±0.1%
- Any
- 290 PSI ( 0 -2Mpa)
- 316L, HC, Tan (Tantilum)
- 4~20mA DC with keystroke and HART, MODBUS
- 1/4“-18 NPTF and 7/16"-20 UNF, 2 -5 ways valve manifold for primary DP flow element (Acone)
- Where multivariables such as flow, DP, temperature, mass flow, etc. used with Acone primary element flow meter
Concept of Mass Flow
Mass flow measurement is the basis of most flow measurement, especially with material balance determinations, and billing and custody transfer operations throughout industry. Oftentimes, measurements are used as indicators of overall process performance. This is due to the law of conservation of mass which states that the mass entering a system is equal to the mass leaving the system when both are measured over the same interval. Therefore, measuring the mass flow rate of a fluid becomes crucial in overall plant operations. The relationship between mass flow and volumetric flow is as follows:
Mass Flow Rate = Density x Volumetric Flow Rate
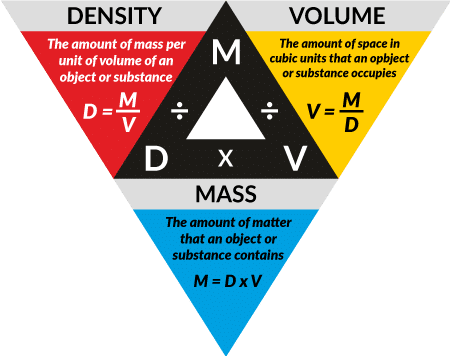
Mass flow meters utilize two distinct flow technologies to measure the flow of fluids, which are thermal and inertial. Coriolis flow meters, a type of inertial meter, apply the Coriolis effect to determine mass flow rate. By inducing apparent rotation into the pipe carrying the fluid, the Coriolis acceleration causes a deflecting force that varies in proportion to the mass flow rate. Thermal mass flow meters, on the other hand, directly mass flow meters measure flow rate of liquids and gasses by utilizing a heating element and temperature sensors to analyze the heat transfer principles.
Volume Versus Mass
The illustration below indicates that while volume can change, mass never changes.
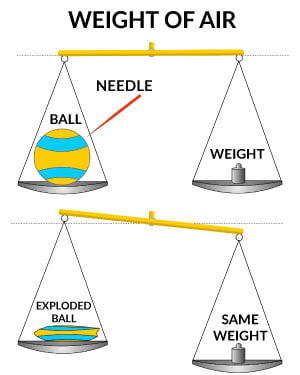
Advantages of Mass Flow Meters
In the past, mass flow was often calculated from the outputs of a volumetric flowmeter and a densitometer. Density was either directly measured or was calculated using the outputs of process temperature and pressure transmitters. Although volumetric flow under nominal conditions may be accurately calculated, the process conditions and fluid properties can vary sufficiently such that it is questionable if the measured volumetric flow rate (or derived using velocity) represents the required mass flow rates. Process conditions such as density and viscosity, and their effect on the accuracy of flow measurement must be taken under consideration. Moreover, each flow sensor adds its own separate error to the overall measurement error, and the speed of response of such calculations is usually not sufficient to detect step changes in flow.
Changes in Process Temperature and Pressure are Automatically Compensated with Direct Mass Flow Measurement
The effects of temperature and pressure on the density of all fluids vary widely. Gas and steam are most affected while solids are least affected, and liquids generally ranging somewhere in between. The effects of pressure on the density of solids and liquids are negligible because both are non-compressible. However, the effect of pressure on the density of gasses is considerable. Viscosity is the fluid property that determines how freely fluids flow. A substance with higher viscosity has a higher resistance to flow which obviously affects flow rate. Generally, changes in the temperature of a fluid inversely affect viscosity.
Direct Mass Flow Meters are Newer Flow Technologies
Direct mass flow measurement is a relatively new measurement technology compared to volumetric ones and it is the reason that most process automation measurement still use volumetric techniques. Today process engineers are requiring more mass flow measurement than volumetric techniques wherever they can. However, the apprehensions of using mass flow versus volumetric flow measurements are based on cost or application where direct measure mass flow is not possible due to various application complications.

Mass Flow for Gases the ATMF series
The Smartmeasurement ATMF series of mass Flowmeters are thermal dispersion type, utilizing constant temperature difference method of measuring Gas Mass Flow Rate. It contains two reference RTD sensors clad in a protective 316SS sheath. Featuring direct mass flow for gasses with wide turn-down of over 100:1, low pressure drops, low flow sensitivity and no moving parts. The ATMF series comes in insertion and inline styles with various analog and digital outputs. It also comes with approval for explosive environments as well as a low for non-explosive gasses.
Mass Flow for liquids the ALCM series
SmartMeasurement’s ALCM series of Coriolis mass flow meters are the only flow meter technology that measures mass and density directly without the need of other sensors to infer mass flow. Smart Measurement ALCM series of several Coriolis meters offer the perfect choice. In addition, Coriolis meters do not have to be recalibrated to handle different fluids or even process condition changes as these changes will not affect accuracy. The Smartmeasurement ALCM series of Coriolis meters are used in a wide range of applications including process evaluation and optimization, mass/energy balancing, custody transfer, pulsating flow applications and processes where changes in temperature, pressure, density occur.
Mass Flow for Steam the ALVT-mass series
SmartMeasurement’ s ALVT-mass are mass vortex flow meters for steam applications which are designed with multiple sensors to detect not only the vortex frequency, but also the temperature and pressure of the process fluid. Based on that data, it determines both the density and the measured mass flow rate. This meter offers a 1% of rate accuracy when measuring the mass flow of liquids and a 2% of rate accuracy for gasses and steam. If knowledge of process pressure and temperature is of value for other reasons, this mass meter provides a convenient, less costly alternative to installing separate transmitters. Learn about our pressure transmitters here.
Mass Flow with Multivariable Differential Pressure the ALDPT-MV with Acone Primary Element
Smartmeasurement’ ’s ALDPT-MV measures three separate process variables simultaneously and provides dynamic calculation of fully compensated mass flow rate for steam and liquids respectively and standard volume flow for gasses. It measures differential pressure and absolute pressure from a single sensor and process temperature from a standard PT 100 Resistance Temperature Detector (RTD). The ALDPT-MV includes flow equations for steam, gasses and liquids so that one model is all you need in your system. It can also measure static pressure with both integral or remote electronics and HART protocol. Many plants calculate mass flow in a host computer using a simplified mass flow equation. The ALPDT-MV provides full compensation of over 25 different parameters to achieve a 5x improvement in flow performance compared to uncompensated DP flow. The ALDPT-MV is ideally suited to work with SMC’s ACONE primary flow element